Microstructures
by
George
Langford, Sc.D., Massachusetts Institute of Technology, Cambridge, MA,
1966
Copyright©2005 by George Langford
Low Alloy Steels - Lesson 3 -
Fourth specimen
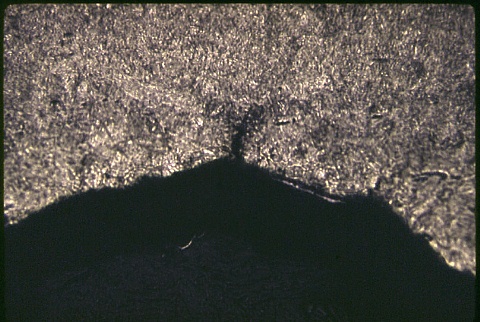
|
Here is a tension member used for prestressing concrete,
made from a 4140 steel, heat treated to Rockwell C45 hardness before
machining the screw threads.
The photomicrograph at left was made at 200X.
The second photomicrograph below this one was made at 500X.
|
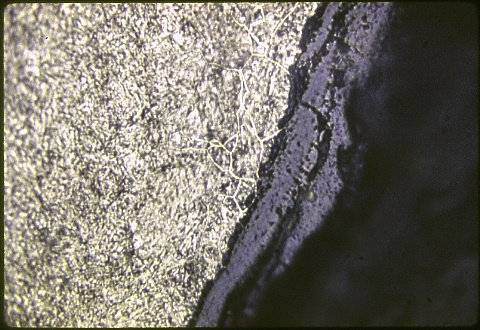
|
Note the ferrite network near the oxidized surface.
This piece broke at low load during tightening and after the concrete
had thoroughly set, ruining the structure.
Why did it break ?
Is there any remedy ?
You can look at the answers once you've
worked out your explanations.
|
Explanation: This is a
quench crack. On the actual fracture surface one could see the
oxidation which occurred during tempering subsequent to the quenching
operation. The fracture surface had a temper color in the portion of the
fracture that took place before tempering and before the final
fracture. The rest of the fracture surface was a metallic
grey. The temper color is due to the formation during tempering
of a thin layer of oxide whose thickness is near the wavelength of
light, about 0.5 micrometers. Only low temperature oxidation (at
200C to 500C) does this. There is no remedy for the failed piece,
but to avoid cracking another one, the quench should be in a warm oil
(50C or so) to reduce the severity of the cooling rate during quenching.
|